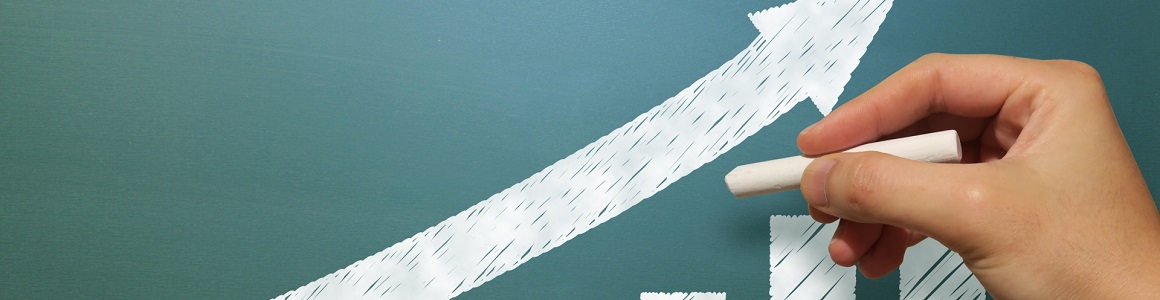
例えばある飲料メーカーの春と秋のキャンペーンの景品を作るとします。主力の飲料ですとチェーン別なのか全国なのかにもよりますが小さい場合では20万個、大きい場合では最大500万個程度を作成することになります。ちなみに有名な「ヤマザキ春のパン祭り」のお皿、あれは1000万枚を大きくこえる枚数が生産されています。フランスの食器ブランドですが、もちろんフランスで作られているわけではありません。中国にいるころ、妻が別の食器メーカーのフランス人と「外国人のための中国語講座」で親しくなっていて、アレにそっくりの「艶あり真っ黒バージョン」をいただいたことがあります。
わたしがこうしたものの生産管理に携わっていたのは5年ほど前までなのですが、当時から大規模なものはすべて中国で生産されていました。逆にいえばこうした全国規模の大規模な販促品を商品にべた付けして配布する形のキャンペーンは中国生産の実現によりはじめて実現したものです。40代以上の方はペプシコーラがスターウオーズのフィギュアをおまけに付けたのを覚えていらっしゃるでしょうか?あのころから「ジュースのおまけ」「缶コーヒーのおまけ」がしばらく盛んになったのですが、これは、複雑な形状のものを中国で短期間に大量に生産することが可能であることが実証されたため広告業界が目新しさから採用した、それにコンテンツ業界も新たな収入源として協力した、というのが背景です。
為替リスクに品質リスク、納期トラブルに高い出張コスト…資金管理に悩まされた私は営業部門管掌で中国の生産体制にも詳しい取締役に相談したことがあります。「同じものを国内で生産したほうが安くなるということはないか?」答えは、「生産設備が国内にはない」ということでした。
中国の工場にいくと1台1億円以上もする高価な金型製作装置が10台も並んでいて24時間体制でスパークを飛ばして金型の加工がされていています。別棟では、日本ではなかなかお目に掛かれないような大型の射出成型装置がこれまた5台並列設置されているような光景を目にしました。日本の中小の工場は概して古くて中が乱雑で汚いですが、中国の海外向けの生産工場は一般に新しく徹底的に整理整頓されています。専従の「清掃工」が何人も大きな工場を一日何周も清掃しているのですから。そこで数百人~1000人以上が3交代で生産を行います。各自の席の上には日本の自動車工場を見習い、手順書が掲示され、検査工程には検査基準が各自の前に表示されています。日本で1000人の工場というとそれこそ自動車メーカーの工場ぐらいしかもうないのですが、中国では沿岸部では一つの街にたくさんありますし、最近では内陸部にも大きな工場が立地しています。
中国の労務費はたしかに上がっています。しかし、これだけの積極的な設備投資を日本の中小の事業者はできません。こんな当てのない設備投資を若者に支援してくれる金融機関は日本にはいません。ちなみに私が最もお世話になっていた工場は、20代の兄弟がオーナーで、1400人の従業員がいましたが、不動産投資に熱を入れ、何年か経って計画倒産させていました。別に非難しているのではなく、やっぱり日本の銀行は貸せません。
そして、1000人もの工員を集めることも日本では相当難しいことであり、1000人となるとそれこそ不織布の帽子や作業服の調達管理、マニュアル配布と講習、給与や休暇管理、それに食堂や寮の運営、中にはけんかやいじめの対処まで一筋縄ではいきません。それを統制をとって運営する経験者も日本にはほとんどいない。いざやれ、と言われても設備だけでなく、熟練工もおらず、それを教育管理できる組織も日本にはないのです。
私自身は500人3交代のCADオペレーションの会社の総経理だったのですが、不良率を下げるのは実は簡単でした。一旦検査を2重にすればよいだけです。そして得られた結果から「検査工程」のルールベースや教育カリキュラムに反映させていき、2次検査での抽出率が十分下がればこの工程を縮小すればよいのです。これも熟練工が100人単位で豊富に確保できるからこそできることでした。
人事部は寮と現場に監視網を張り巡らせ、総務課は寮、工場に起きるトラブルをその場で自力で修理する即応チームでした。経理部だけは、シリーズで紹介の通りいろいろトホホでしたが…日本では体験できない組織運営のダイナミズムでした。
それが今の日本と中国の差です。たとえ労務費が並んで、あるいは逆転したとしても経営者や金融機関のリスク回避姿勢、それに人的資源の不足、という差はそれ以上に大きいのです。中国との人件費水準の差は急速に縮小してきていますが、それでもなお、価格が少しずつ上昇したとしても、あるいは政治的に厄介なことがあったとしても、中国の豊富な人的資源とチャレンジを当然視する金融資源を生かした役割分担というのは当面続かざるを得ない、と私は考えており、それが当社が創業にあたり、再度「中国」とのブリッジを柱の一つとした理由です。
【日本人は何をするべきか】
かつてはいがみ合うこともあった先ほどの営業担当の取締役と最近、またお互い別の立場で仕事面で協力しあうことが再開できました。彼も今は中国へ生産管理に行くというところは他の人に任せているようです。
実は先日、ある企画の件で打ち合わせ終了後に彼に相談しました。具体的には、紙パルプを圧縮して作った板状のものに2色印刷を行いたい。それをできれば内製化したい、ということでした。するとよどみなく、方法論を列挙し、必要設備を列挙し簡単に評価を述べ、私が例示した方法よりも他の方法の方が適している可能性が高いこと、設備投資とコストの関係を私に指摘しました。
彼は一年の半分近くを中国に行っていたので当時は「この人一体なにしてんだろう」と怪しんでいたところもあったのですが、制作を発注した者に対して工場の採用する方法論とその工程が適切に行われるかを見て回っていたその実力がこの時如実に現れていました。結局作業を中国にサンプルを送って「これを作りたい」と依頼することはできても、どのような品質を要求するのか?そのためにどのような工程を用いる必要があるのか?あるいはトラブルを避けるためにはどのような工程管理と輸送管理をするべきか、そしてそれらが工場に行ったときにそれが適切に実施されているのか?はどんなに中国が大きな生産力を保有していても、彼のような人間がそれを理解し具体的に指示しないとうまくいかなかったのです。
中国はそろそろ、アメリカのクリスマス商戦向けの生産が大詰めです。船で日数がかかるので、この時期はどこも大忙しです。それらの商品は日本向けよりも単価は高く、品質要求水準は低く、数量は日本向けより一桁多いため、どうしてもそちらの生産が優先され、あちこちで日本向けの納期遅延が起きます。でも彼の管掌する工程ではそれは起きていませんでした。
日本で使われる商品、あるいは日本で企画し世界に発売する商品は、これからも大半が中国で生産されるでしょう。しかし、その生産技術や管理手法を知らない人が発注すると、出来上がってくるのが「中国のやすかろう、わるかろう」の商品なのです。日本にはないような最新の設備を理解し、技術を指導し品質を作りこむ技術者は結局必要であり、それを本来は日本で育てるべきであるし、それがもうできない組織であるならば中国で日本人を学ばせなくてはならない時代になった。というように考えています。