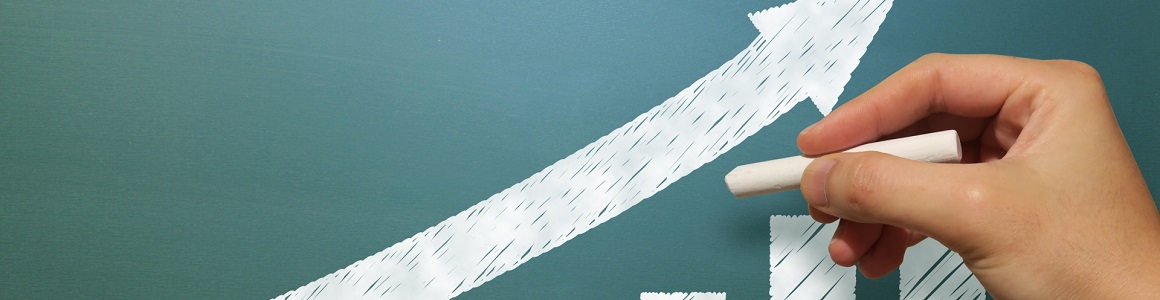
今回のお話しは中国で生産管理をしている人には当たり前すぎる話なのですが、そこに関わっていない人、そもそも生産管理自体を知らない人にとっては、「へぇ」と言ってもらえる話であるようです。
最近、説明する機会がありましたので、この機会にまとめてみました。
①中国 VS 日本
日本では「モノづくりの基本」の知識が製造業の現場で従事する人は別として、多くの働く人からはすでに失われてしまっています。
「日本は品質が高い」「それはモノづくりに誠実な国民性がなせるものである」という「伝説」がメディアを中心に信じられていますが、最近もものすごくいい加減な工程管理のために製品の利用者に死者が出てしまった北陸の製薬会社があったように、別に日本人だけが特別誠実で、特別丁寧ななわけではありません。また、日本の方が生産性は高いのに、労務費に起因するコスト競争力で負けているという人もいますが、それも正しくありません。日本の小規模な工場に比べると中国の(沿岸部の比較的大規模な)工場は、設備投資が進んでいて、最新鋭の機械とITによる生産管理を導入して、品質も生産性も高い傾向にあります。
むしろそのために、設備の減価償却費が増大し、昔ほど安くないことと、生産性の大幅改善に伴い大ロットでないと、コストメリットが出にくい傾向が強くなってきています。かといって、日本では少し大きな数量で物を作ろうと思っても、短期間でできるところがありません。今はもう状況がだいぶ違っているのです。
②工場経営者と管理者
中国の工場にいくと、高卒の作業員を大卒の若い管理者が一日、特に何もせずに監視し、時々偉そうに叱っている光景を目にしますが、実は彼らは生産管理手法やデータ分析などの基礎的手法に日本の工場関係者よりもはるかによく知っています。そういう実用的な教育を受けているし自分でも熱心に勉強していて、日本から「工場監査」に来たおじさんたちの不勉強であいまいな質問を内心バカにしています。
2005年頃から、中国では工場で労務費が高騰し、同時に環境規制がどんどん厳しくなりました。そのため、特に沿岸部を中心に改善意欲と資本力のある工場にどんどん生産の集約が進み設備の自動化が進んでいきました。2010年の時点ですでに、日本の工場では1台入れるのも大変な高価な金型加工装置が10台並んで24時間自動で金型を加工し続けているような光景が中国では見られていました。ちなみにこの時に淘汰された企業のうち、かなりの部分は、日本、韓国、台湾などの外資で比較的早期に進出していたが、中国の環境変化に対して、投資を拡大し生産し続けることに経営者の腰が引けていた企業です。逆に残っている会社は、設備投資や生産手法の革新の必要性を認識し、それを実行してきた会社です。
これは、中国と日本だけでなく、中国と台湾でも同じで、旧型の設備、高齢の従業員を抱える台湾の工場が意外にも中国よりもむしろ安い、という事が最近では、あります。古い設備を酷使しながら、ベテラン老板(ご主人)が必死でやりくりしている「町工場」があるのですが…こういうところは、不良や部品欠損の問題が多く、検査機械を買って導入してくれ、と要求してもなかなか対応できなくて、「今後、気を付けて検査します」と典型的ダメな品質管理回答をしてきます。人を非難しているのではなく、生産システムを改善してくれ、と言っているのにそれをわかってくれない、というのは日本でもよくある話です。
③品質とコストのトレードオフ
どこの国であっても製造方法や品質管理手法は、短期的に同じ工場では、常にコストと品質がトレードオフの関係にあります。そのため、顧客から特に何も指定がなければ、「常識的な不良率の範囲でコストパフォーマンスが最大になる」方法を工場は選択します。
これは工場全体としてだけでなく、そこで生産に携わる個人においても同じです。中国では(日本以外ではと言った方が正確かもしれませんが)、個人の生産数量が給与の成果給に如実に反映され、基本給が最低賃金等の法的規制ぎりぎりで、成果給が固定給の2倍、3倍というケースが普通です。もちろん、そこから「不良を発生させたら、生産量の2倍をペナルティとして差し引く」というような品質インセンティブを設けているのですが、それでも少しでも生産量をあげて、給与を増やして、貯金して、そのお金で夜学校に行って英語や経理を学んで工場労働から抜け出す、という事に彼らは必死です。このことが、日本に比べて中国が圧倒的に生産性が高い理由の一部でもあり、同時に品質基準ぎりぎりの製品を生む理由でもあります。
100円ショップの製品の、使用に問題のないようなムラ、傷にまでクレームをつけ、交換させ謝罪させる日本の消費者は、世界でも異常な存在です。私は最近、ヨーロッパ製の生活雑貨のコンテナ輸入にもかかわっているのですが、品質レベルは中国生産と同じです。これが世界の標準なのであり、日本だけが別基準であることが結果として利益を減らし、あるいはコスト競争力に優れた生産委託先から断れるなどの不利益を生んでいることはもっと知られるべきだと思います。まあ、経営は市場を正として対応を考えるゲームですので、市場に文句をつけても仕方がありませんが…
品質を改善するには、次のような方法を取ります。
しかし、最も必要なのは上のいずれでもありません。それは、「具体的な要求をきちんと、少し強い口調で伝える」という部分です。日本の慣れないバイヤーを見ていると、日本的に「相手にも品質を良くしたいという良心があるだろう」とか「自分の思っていること、困っていることをきっとわかってくれるだろう」という態度をとっている例が見られ、要求のための資料作りや調査勉強を怠り、「なんとなくお願い」で済ましていて、それで「中国はダメだ」と言っている事例が多くみられます。
これは中国だけでなく、世界中で通用しません。けんか腰になってはいけませんが、まずは自分の要求を明確に伝えなければ何も始まりませんし、日本もビジネスの現場で国籍やバックグラウンドが多様化してきている中で、これではもう通用しなくなっています。「こんなこと言ったら嫌われるかな、バカにされるかな」というような遠慮をしていてはいけない時代になったのです。