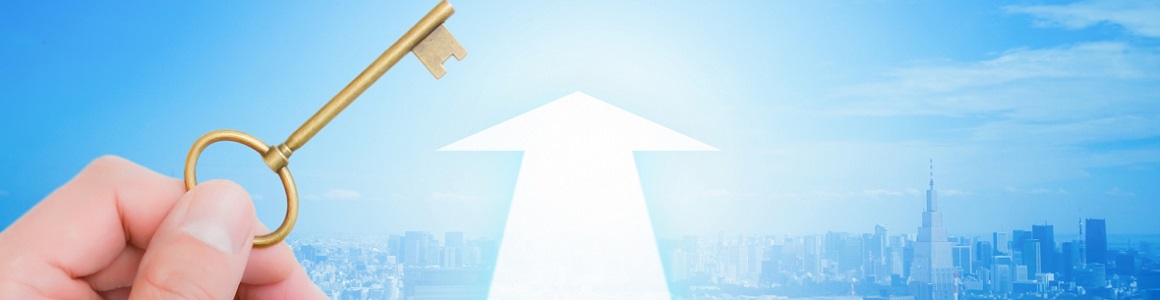
会社を運営していて本当にいらいらするのは、受注できないことでもなく、経費を無駄遣いすることでもなく、「言ってることややっていることがことごとくいい加減であいまい、確率も時期も正誤もあてにならない」ことです。だいたいこういう会社は業績が悪い。それが当たり前の空気になっていて、しまいには「営業は水物」と営業自身が言っているのを経営者が手のつけようがないと放置しているために、みんながそれが許される空気に怠惰に流れています。あてにならない仕組みのまま放置しているのは他ならない経営者のあなた自身です。
変えるにはどうすればよいのか?という処方箋も、このシリーズの方法論にあります。決められた手順の確立と部分ごとの品質管理、それと定点観測的なデータに基づく業務管理と評価です。
前回は、業務の中で各手順がどのくらいのコスト(時間)がかかっていて、どのくらいの確率で成功しているのかを計測した上で、共有可能なプロセスを一か所にまとめてしまうことで重要箇所の集中改善を進めるということをご説明しました。前回はこちら
今回は、その続きの「プロセスの改善方法」について説明を続けます。ただ、実は今回ご説明する内容は、これまでの「一業務の全体」をとらえて分析した箇所と方法論的には同じです。同じ手法を全体に適用したうえで、さらに部分にも適用する、ということです。(だから誰にでも運用できる方法論なのです)
8 業務を構成するプロセスの手順と品質基準を明らかにする。これができるとチェックリストもできる。
まず、これからご説明します。業務にインプットとアウトプットがあり、その中にいくつかのプロセスがあって分解したように、業務を構成するプロセスの中にも手順があります。業務をプロセスに分割する時には、中間生成物や、準備・実施・チェックのプロセスに分けて分解したわけですが、プロセスを分解する時には、手順を順番に書き出すことになります。それは、「他の人がやっても同じようにできること」のように記載します。ただし、そのように記載しても、最終的には、事務仕事には、「連想」「発見」などのルール化が比較的難しい要素が残ることがあります。それはもうそのままでよいです。徐々にパターンを蓄積することで誰でもできるようにすることはできますし、そこまでいかなくても、「個人によって力の差がある」ことは事実であり、「必要な箇所には力のある人を配置する」「力のある人を採用し、優遇する」(そうではない人は冷遇される)ことは「そうですよ」と言わざるを得ない部分が残ります。
よく、このような文書化プロセスを説く人は、「誰でもできるように」するということを目的として言います。それができればもちろん一番よいですが、人材にばらつきがある中ではそれは実際にはできないことです。概ね社員の中で半分が対応できるレベルでよいとしないと永遠に次に進めませんので、そこから先は人事制度で対処することが適当です。
で、ある程度は誰でもわかるように手順を書いて、その途中でも「チェックポイント」「チェックリスト」を設けます。これは業務全体のアウトプットにチェックリストを用意したのと同じです。ただし、あまり同じチェックを何か所もやっても時間の無駄ですので、過去に問題が起きた箇所-そのうち一部はきっとインプットデータに起因するものなのですが-を中心に担当者が初心者に教える際に点検する箇所を中心にリストアップすればよいでしょう。それらのチェックを通過できることがそのプロセスでの合格基準ということになります。
この途中のチェックポイントは、①業務の最後まで行ってからエラーが発見されて手戻りの時間が大きくなるのを途中の段階で阻止する。という効果のほかに、②特に初期には、様々なエラーが混在して何から工程を改善したらよいかわからない、という状況を鎮静化させる という意味があります。
もちろん、こんな「当たり前のこと」を書類にして、それに従って毎回作業することは作るだけでなく、作業する過程でも面倒なのですが、たいていのクレームであとから責任者が「アッ」と絶句するトラブルはこうした「知っている問題」を見逃すことで起きています。そして、トラブルが起きてそれに対応するコストは、そのチェックする工程を省くことによって得られるコストの節減の何十倍もあるのが通常であり、かつチェック工程を義務化することで熟練工である必要性が薄れることによる人件費のコストダウン効果が得られます。そのため、多くのケースでは途中のチェックは正当化されることが多いのですが、検出量が減ってきたら、その際には工程を簡略化して生産性をあげることも考えることになります。つまり、毎回チェックすることが重要なのではなく、チェックしても修正が検出されないよう工程自体を改善しき、最終的にはチェックを減らしていくことで生産性は上がっていくのです。
こうしてチェックができる体制ができたら次の段階に移ります。次は
9 プロセスのうち、時間がかかっているもの、品質が悪いもの(ボトルネック)を洗い出し、そこの改善を集中的に取り組む。その間、他の個所は気にしなくてよい。これにはソフトウエアによる自動化を含むが、5~8の過程で自動化の対象や内容は明確になっている。
に進みます。7で大雑把に時間を計測してもらいました。そして、8ではチェックリストを作ってどうしても修正がたくさん発生する箇所を見つけられるようにしました。ここに至って、ようやく「改善すべき工程」が誰からも客観的にわかるようになりました。前回記載のような「間違った着手」はこの段階でようやく防げるのです。
ところで、多くの会社の改善プロジェクトに携わる中で私が思うのは、「全容把握」や「データ収集」に目標期間の半分程度を投じてよい、ということです。これは、まったく着手しなくてもよい、というわけではなく、ある程度の試行錯誤の中からわかってくる事実がある中で一部を先行することはあってよいと思います。
このシリーズでは、「ルーチーン業務」の改善プロジェクトを取り扱っています。だいたい、ルーチーンが業務の8割以上でないと会社は安定しませんので、「うちはベンチャーなのでルーチーンなんてありません」という会社は、私は「危ない会社」(ということは私にとっては顧客候補ですが)だと思っています。しかし、その中でプロジェクトの準備、段取りに時間をかけない、ということがだいたいプロジェクト進行の下手な会社のよくある状況です。全体が洞察できる状況を、全体計画を修正できるできるだけ早い段階で作るためには、初期に相当はやる気持ちを抑えて準備と調査に時間を割く必要があるのです。
あるプロセスを改善するには、チェックリストだけでよいのではないか?と思われるかもしれません。確かにそれでエラーが後工程へ、そして顧客へ流出する状況は阻止できます。しかし、それがなぜ起きるのか・それが起きないようにするにはどうすればよいのか?を工程に加えないと、いつまでもチェックリストでチェックされ、手戻りして修正するコストがかかり続けます。この理屈は、製造業での工程改善に携わった人には当然のことと思ってもらえるのですが、それを知らない人にはなかなか納得していただけないことです。
そもそも「オペレーショナルエクセレンス」つまり、日常の業務が低コストで高品質である状況が安定して持続する状況を作ることが目的でしたので、チェックリストを作って品質安定化をすることはその一部にすぎません。究極の目標は、チェックをしなくても何の問題も起きない状態にすることですし、もっと言えば人ではなくコンピューターがすべてを無人で間違いなく、瞬時にやってくれることです。どうすればそこに近づけるのか?を考えていくことが必要なことです。
では、どのような改善方法があるのか?それはどのように見つけるのか?について次回ご説明していくことにしましょう。